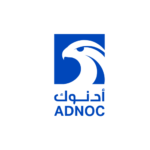
ADNOC
http://adnoc.ae
+971 2 707 0000
The role of Maintenance Team Leader at ADNOC is to lead, guide, coordinate and supervise the maintenance support activities of a wide range of Plant Automation systems, Telecom and Fire & Gas Systems. ensure safe and reliable plant operation and minimize equipment down time and improve productivity. Support and supervise all Automation, Fire & Gas, Telecommunication related to design and engineering activities for Project studies and proposals. Job ID for this vacancy is 23271.
Responsibilities Of Team Leader Maintenance
- Lead and manage the day-to-day preventive, corrective, breakdown maintenance activities.
- Ensure cost-effective solutions and value addition throughout their assignment.
- Ensure effective implementation of shutdown maintenance programs and modifications so as to achieve enhanced plant safety, availability & reliability.
- Prepare Team’s Capital, EOM, MM and Operating budgets and monitor/ control expenditure against budget.
- Lead the team for effective failure analysis, bad actor’s identification, conduct RCA’s for plant reliability improvement.
- Guide the team to develop solutions for problem resolution, plan and implement the solution in a time bound manner.
- Ensure efficient use of resources with the aid of system.
- Develop & implement maintenance strategies for the Plant Automation systems assets in line with work request and required target.
- Provide technical inputs to various upgrade and obsolescence issues being addressed by the maintenance group.
- Assist maintenance group for effective implementation of various Automation systems, Telecom and F&G systems upgrade/replacement projects so as to maintain the system high availability , safety & integrity.
- Provide technical input for expansion projects activities and participate in HAZOP and SIL studies.
- Ensure that Instrumentation system deficiencies are addressed in the project stage to integrate the expanded areas with the existing facilities.
- Liaise with Mechanical, Electrical, I&C & Planning teams and establish a seamless integration between operation and maintenance teams.
- Ensure development and implementation of Management of Change request by participating in site engineering studies.
- Determine the feasibility of introducing modification to enhance system reliability and efficiency of plants.
- To direct and coordinate the activities of a team of multi-disciplinary technical experts in the team.
- Ensure the proper maintenance of the Automation systems, Telecom and Fire & Gas Systems of the plant.
- To lead team to establish Long term service agreements & maintenance contracts for various outsourcing activities.
What You Will Do More As A Maintenance Team Leader
- To review equipment history data, analyse chronic failures and problems, identify frequent ‘bad actors’, conduct Root Cause Analysis.
- Develop recovery strategy for the implementation of upgrades and modifications to improve reliability.
- To propose, develop and implement Management of Change (MOC).
- To enforce the implementation of ADNOC Sour Gas Health, Safety and Environment Management System (HSE-MS) and asset integrity reliability management system (AIRMS), and promote awareness of its use among his staff.
- To monitor maintenance activities and identify opportunities .
- Improve the performance of Plant Automation systems including advanced applications, Fire And Gas field devices and Telecom systems
- To ensure the maintenance and security of control software related to Automation system backups, and policies and procedures manuals.
- To ensure maximum utilization of the SAP, CMMS system for equipment history and data analysis.
- To ensure implementation of competency based Training & Development programs, through use of Development Plans (PDP/ CAMS) and UAE Nationalization directives.
- Lead the team for effective failure analysis, bad actor’s identification, conduct RCA’s for plant reliability improvement.
- Guide the team to develop solutions for problem resolution, plan and implement the solution in a time bound manner.
- Ensure efficient use of resources with the aid of system to develop & implement maintenance strategies for the Automation system assets in line with work request and required target.
- Provide technical inputs to various upgrade and obsolescence issues being addressed by the maintenance group.
- Assist maintenance group for effective implementation of various system upgrade/replacement projects so as to maintain the control system safety & integrity.
- To control and authorize implementation of system modification in the Automation systems through Integrated Control Systems Modification Requests(ICSMR).
- Provide support to ensure compliance to Plant Automation systems OT cyber security standards as per ADNOC guidelines in coordination with ASG HQ and ADNOC OT cyber security division.
Additional Responsibilities
- Provide support to maintain all advanced application including Advanced Process Control (APC), Process Data Historian (PHD), Advanced alarm management(AAM), Laboratory information system(LIMS), Operator Training simulator (OTS) and Process safety Analyzer (PSA).
- Take a lead to maintain Telecom systems including TETA radio, Public address , Access Control , Process & Security CCTV, PABX , Fiber optic cabling , Telecom Network infrastructure.
- To provide technical leadership to telecom team members.
- Interface with HQ IT team to ensure coordinated support for PABX, IT infrastructure on telecom network, PHD data interface with servers in HQ and PHD clients supports at site.
- Provide support for effective alarm management in coordination with I&C, Operations and Process engineering teams as per the Alarm Management standards issued by ADNOC GAIPS Division.
- Monitor and control spares inventory in coordination with Procurement Division by analysing the stock level and rate of consumption.
- Provide guidance and advice on Automation, Fire & Gas and Telecommunication design and selection aspects for projects, studies, proposals, upgrades, modifications, modernizations, revamps, expansions and repairs and extend the required support and assistance during plant commissioning and start-
- Ensure development and implementation of Management of changes (MOC) by participating in site engineering studies.
- Determine the feasibility of introducing modification to enhance system reliability and efficiency of plants.
- To provide technical inputs to major and minor projects and extend the required support and assistance during commissioning and start up.
- Participate in HAZOPS, SIL classification and reliability improvement initiatives to ensure the incorporation of lessons learned and the minimization of production risks in the short and long term.
- Perform other similar or related duties, as required.
Responsibilities Continued
- Compile and provide input for preparation of the Department budgets.
- Regularly monitor expenditure against approved the team budget levels.
- Investigate, highlight and reconcile any significant variances to ensure effective performance and cost control.
- Lead the implementation of approved team policies, processes, systems, standards, procedures and internal controls.
- Support execution of the Department work programs in line with Company and International standards.
- Implement the Company Performance Management System for individuals within the team in accordance with Company approved guidelines.
- Continuously monitor the achievement of the Team KPIs related to the approved Annual Performance Management Contract and the Balanced Score Card.
- Review, develop and recommend the appropriate organization structure for the Team.
- Best utilize human capital while proactively incorporating sustainability into the on-going work practices to meet the business objectives.
- Encourage innovation, enhance employee motivation and support initiatives for implementation of Change Management to continuously improve operations and services.
- Propose improvements in internal processes against best practices in pursuit of greater efficiency in line with ISO standards in order to define intelligent solutions for issues confronting the team.
- Support the institution of an HSE culture and ensure compliance with relevant HSE policies, procedures, systems & controls and applicable legislation and sustainability guidelines across the team in line with international standards, best practices and ADNOC Code of Practices.
- Ensure adequate HSE training and induction for all team employees to meet HSE standards.
- Prepare all the MIS and progress reports to provide accurate and timely reports and necessary information to Company Management to effectively manage the business.
Minimum Requirements
The eligibility requirements for the role of Maintenance Team Leader are as under:
- Bachelor’s degree in in Electrical /Electronics/ Instrument / Control Engineering or equivalent.
- 10 years’ experience in the Plant Automation, control systems and Telecom systems Design / Maintenance support in an oil/gas or petrochemical industry, including 5 years in a supervisory position.